Top 7 reasons to use MakerBot Materials with METHOD
1. EACH MATERIAL IS TESTED AND OPTIMISED
Once the decision is made to optimize a new material for the METHOD platform, we work with a material supplier to get samples and suggested settings. From there, a collaborative effort between our software development team and test engineering group will develop and optimize slicing profiles that will yield best results in part quality, surface finish, dimensional accuracy, and print time. Depending on the material type, this process can take up to several months. You can download our free 30 page 3D Printing Materials guide here to learn more about the different materials for METHOD.
2. THE MATERIAL IS TORTURE TESTED TO ENSURE QUALITY
During the optimization, ABR tests are conducted across dozens of printers to ensure consistency of these settings while printing some of the most challenging geometries. These tests can be gruelling and push the printers to their limits to find the limits of both the hardware and the material, and ensure the user will have a good experience when they print with the new material.
3. SENSORS ARE LOADED INTO SPOOL FOR OPTIMISATION
Once the material is manufactured, it is spooled up and bagged. METHOD utilizes the Smart Spool system, which is a purpose-built spool that contains sensors read by the printer when loaded into the material bay. The RFID chips contain information about the material type, color, amount remaining on the spool, etc. This information allows the printer to use the optimized print settings with the material type, further streamlining the user experience. The spools are shipped in resealable mylar bags, which are impermeable to light and moisture and help protect the filament from potential damage. Within the spool there is also desiccant to keep the environment moisture-free.
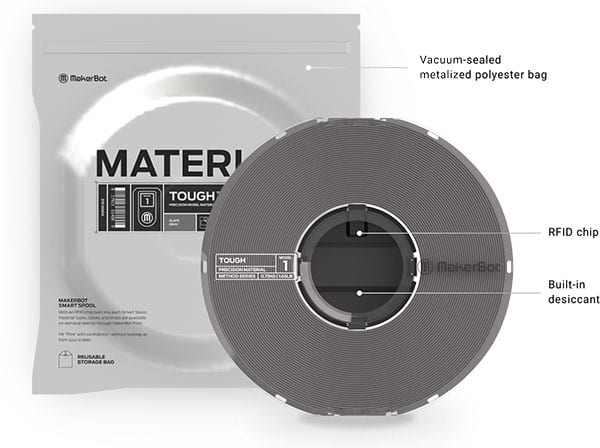
4. HANDS FREE SMART ASSIST MATERIAL LOADER
Once the spool is loaded into the drawer of the material bay, you only need to insert the tip of the filament into the material slot. The printer recognizes the presence of filament and will do the rest of the work loading the filament up the routing tube and into the extruder. This hands-free process is not only convenient for users but also prevents the user from accidentally adjusting a calibrated extruder
5. DRY-SEALED MATERIAL BAYS PROTECT THE FILAMENT
3D printing in even a remotely humid environment can negatively impact print quality, compromise reliability and part dimensional accuracy. METHOD utilizes dual material bays that are sealed from the outside environment to protect your filament from exposure to damaging humidity. Once material starts loading, the drawers on the material bays can be closed. The two Dry-Sealed Material Bays are sealed from the outside environment. This seal, combined with the desiccant cartridge of the Smart Spool, ensures that the material is stored in a low-humidity environment even during printing and in between prints. A sensor in the bay can show the humidity level within the bay and humidity levels can be tracked across Smart Spools. Protection from humidity is especially important when printing with materials like Nylon and PVA – both of which are prone to absorb moisture which can cause damage to the end print

6. SPOOL DRYING FOR PERFECT PRINTS
METHOD has the ability to dry spools using the heat within the Circulating Heated Chamber. To run this function, use the touchscreen to navigate to Settings >Advanced and select Dry Filament. To take it one step further, get the Material Dry-Kit which includes a fresh bag and fresh desiccant. Putting your spool into the kit before running the dry cycle will improve the results significantly. The Material Drying mode revives old spools and allows METHOD to work reliably and accurately from the lab to factory floor.
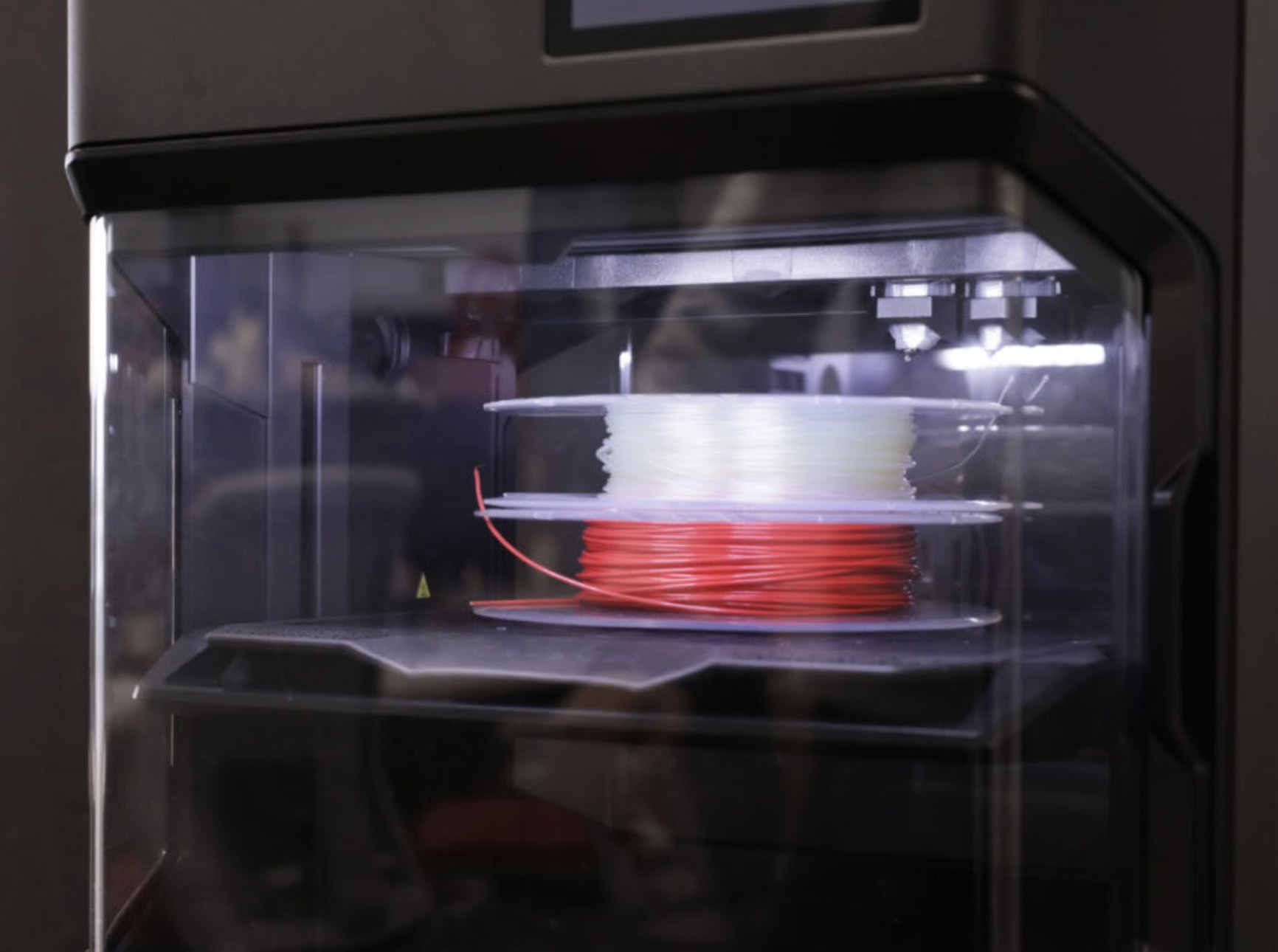
7. PERFORMANCE EXTRUDERS SENSE MATERIALS
METHOD has two extruders – one for model material and one for support material. These extruders are packed with a sensor suite and chip set that enable them to accurately control print temperature so as not to damage materials. The sensor suite also includes active jam detection, and auto- stop when filament runs out. With a range of temperatures, METHOD’s extruders can handle higher temp materials such as ABS and ASA, or when active cooling is turned on, single extrusion low temp materials can be printed with ease.
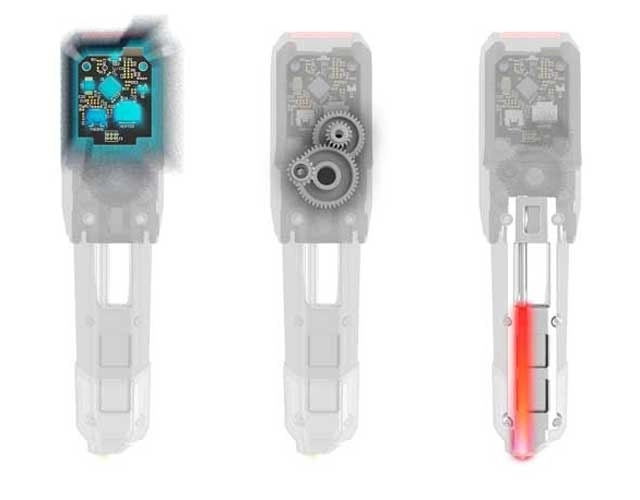
WHAT ABOUT PRINTING WITH NON MAKERBOT FILAMENT?
After learning all about the top reasons to choose MakerBot Certified Filament on the METHOD platform, if you want to use a non certified third party filament, read on. You can print on the METHOD platform with non-MakerBot filaments in most cases. However, we recommend sticking to genuine MakerBot certified filament for ease of use, proven results and warranty protection. Read more about how to print using non-genuine MakerBot filament here
Recent Comments